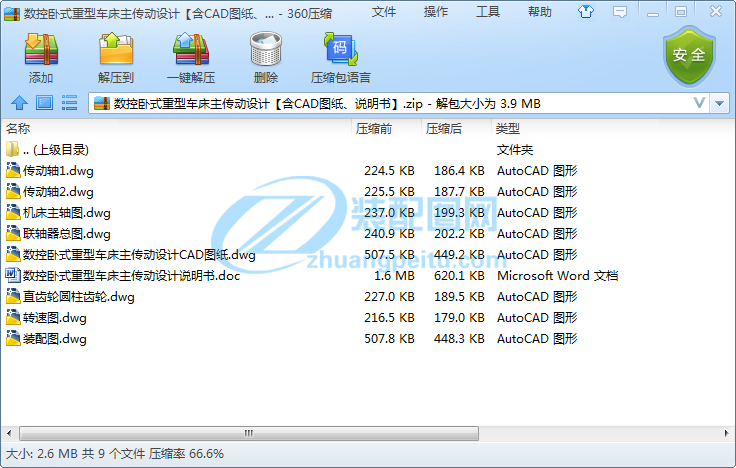
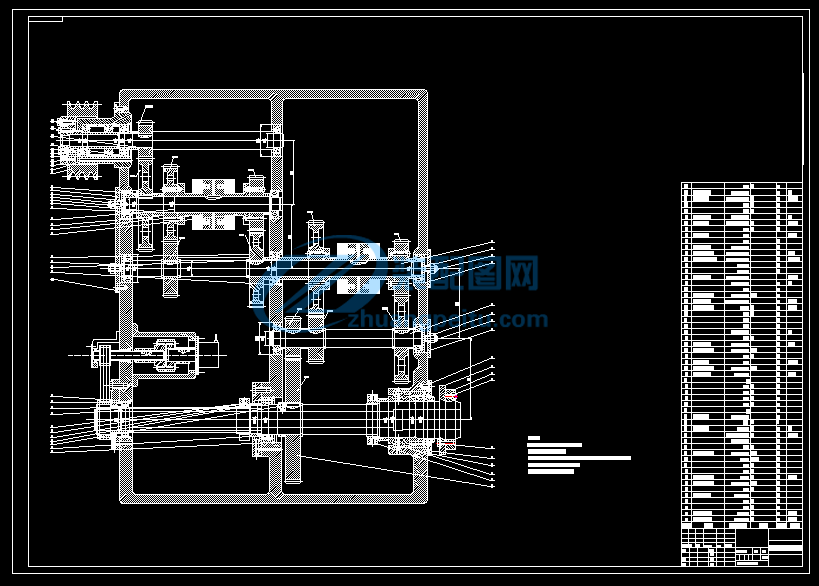
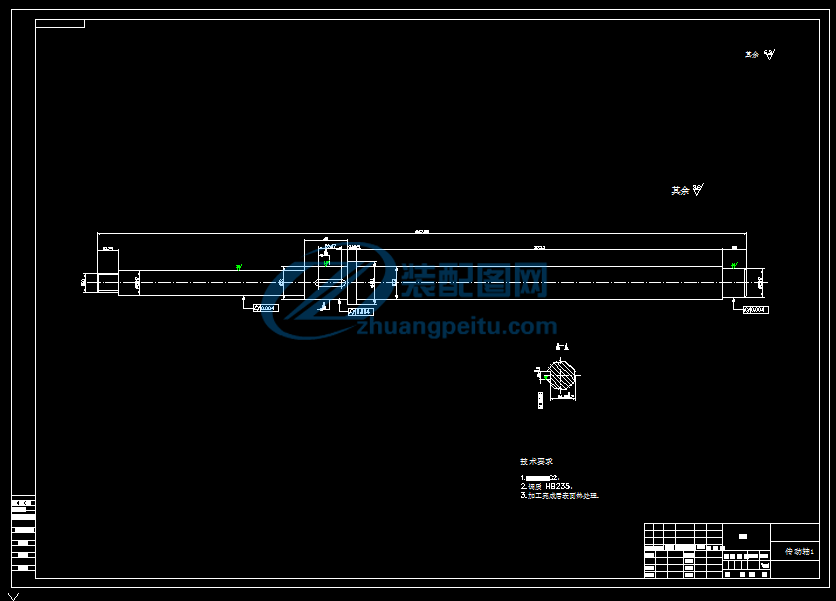
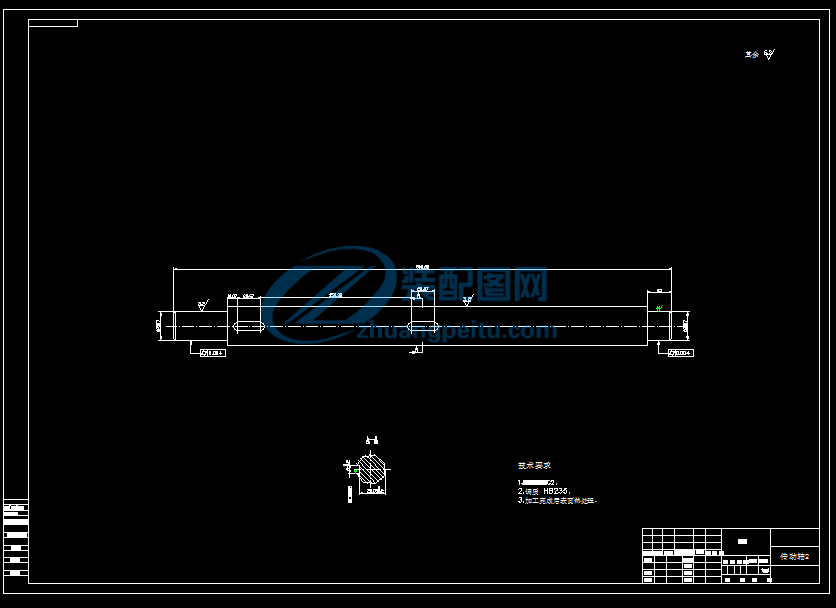
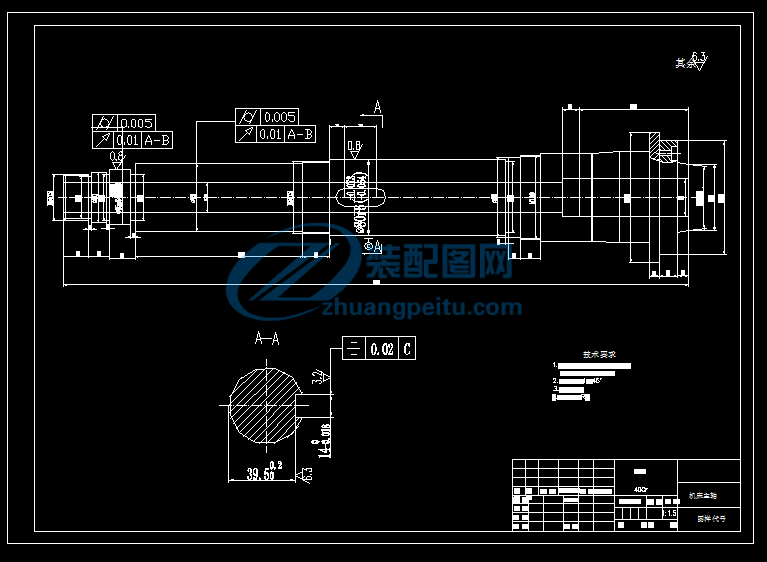
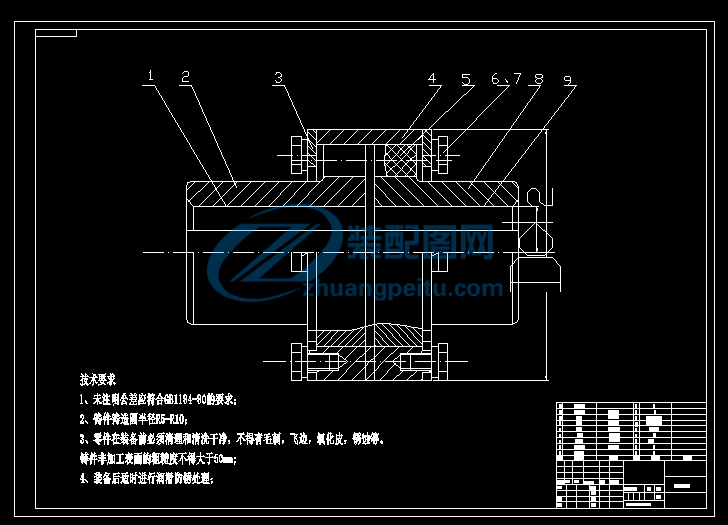
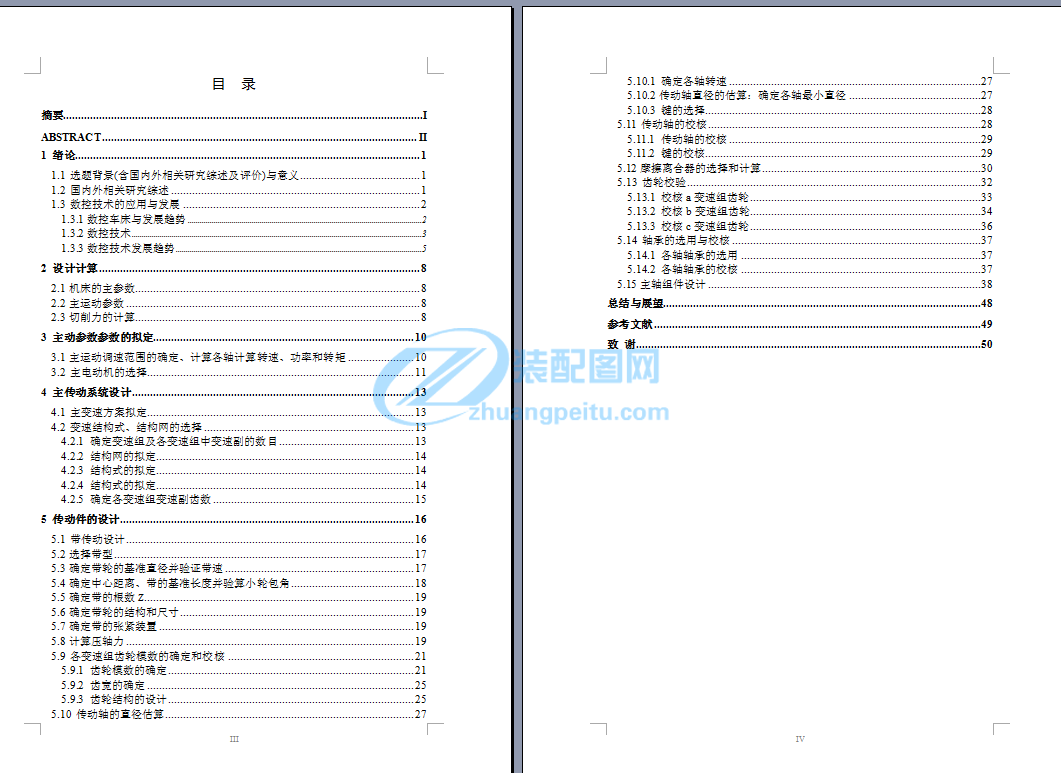
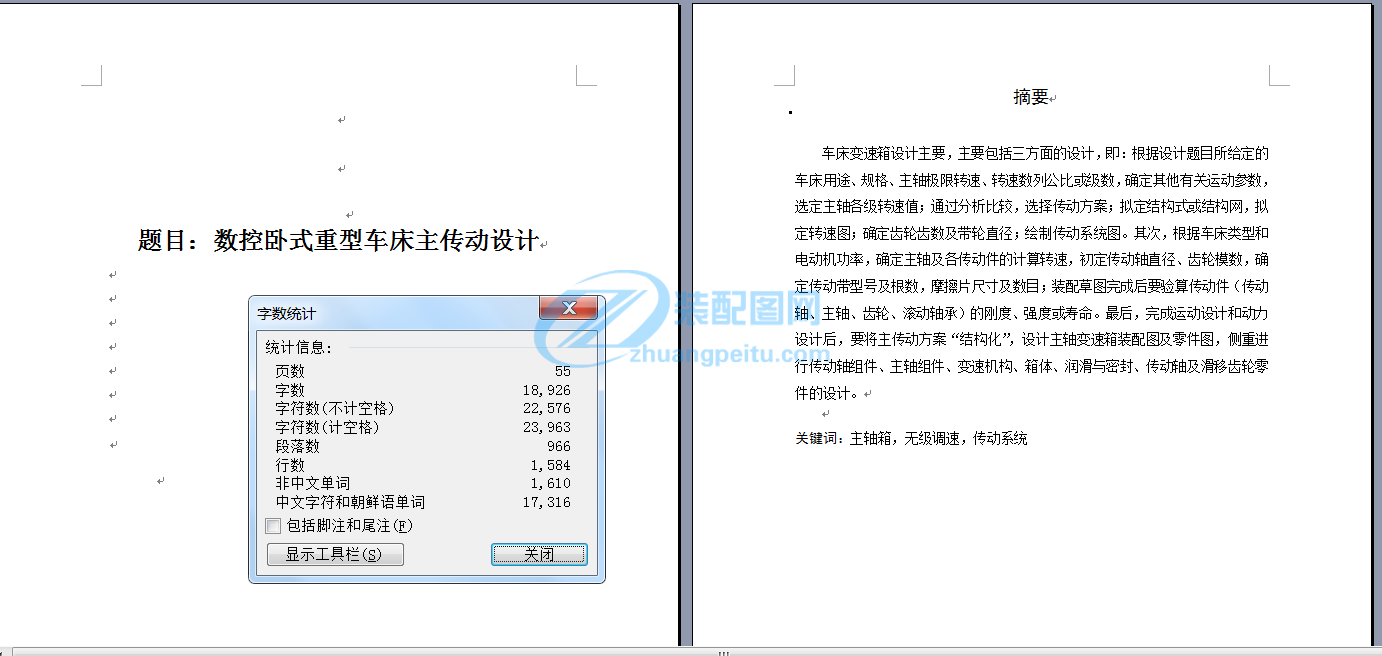
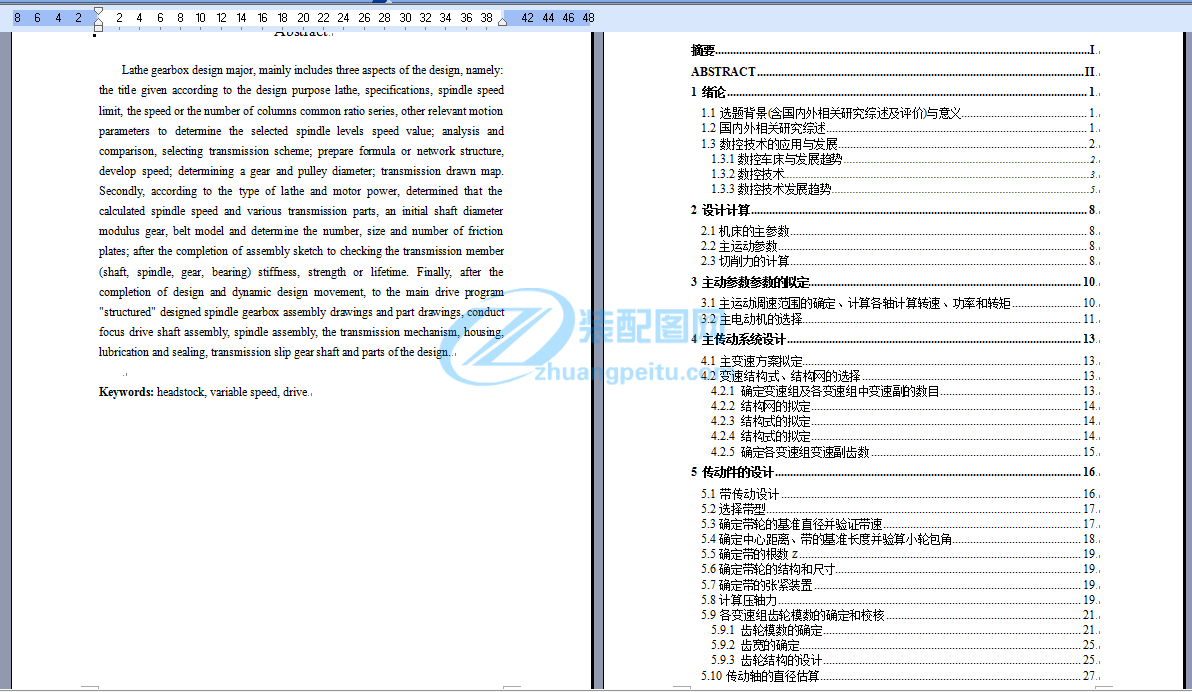
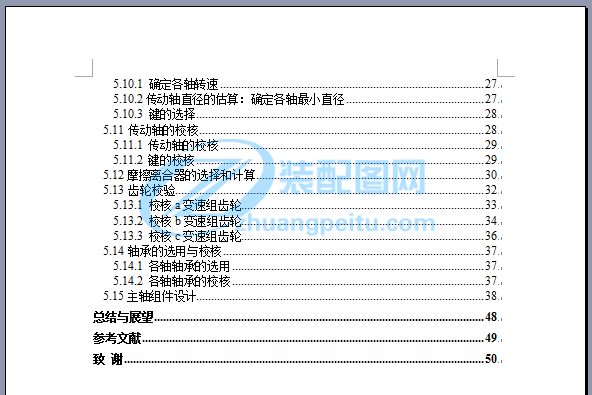
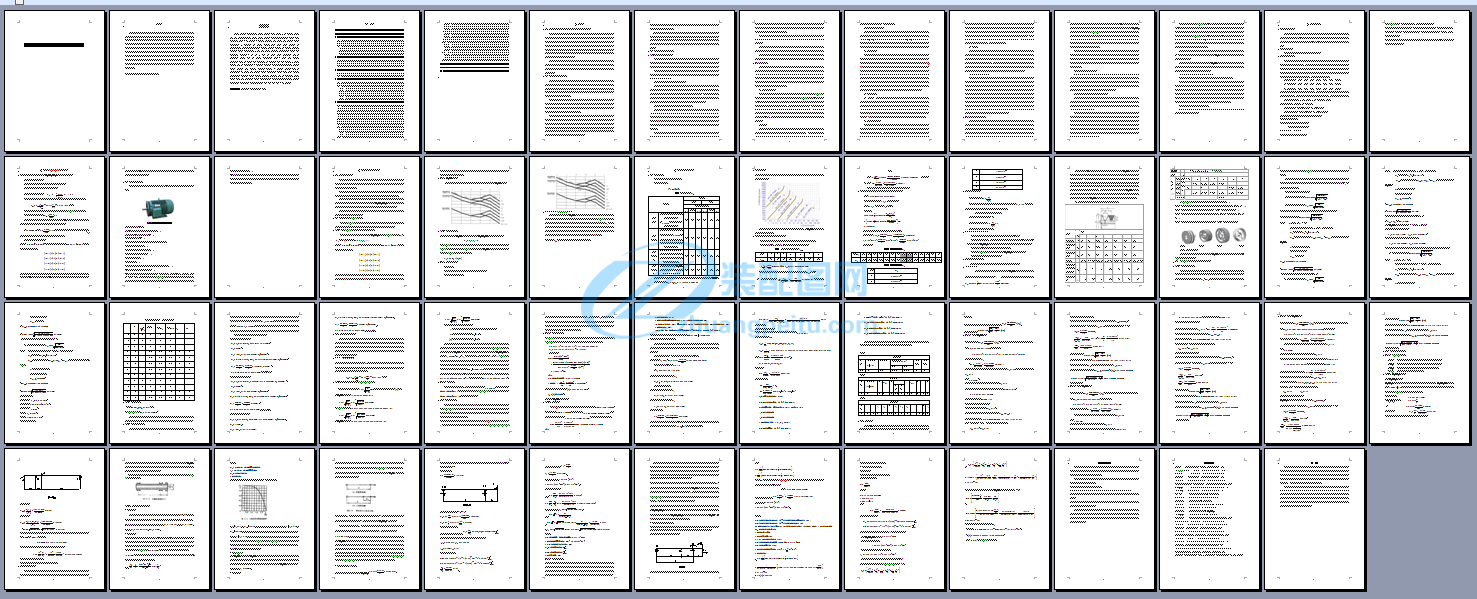
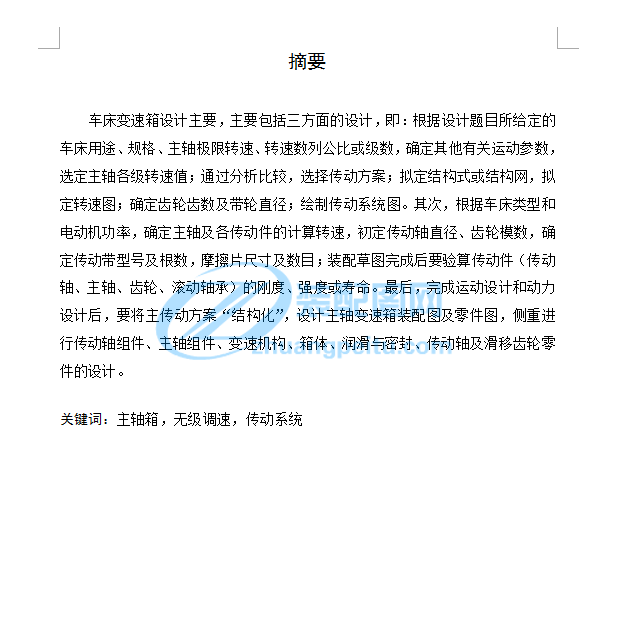
題目:數控臥式重型車床主傳動設計I摘要車床變速箱設計主要,主要包括三方面的設計,即:根據設計題目所給定的車床用途、規(guī)格、主軸極限轉速、轉速數列公比或級數,確定其他有關運動參數,選定主軸各級轉速值;通過分析比較,選擇傳動方案;擬定結構式或結構網,擬定轉速圖;確定齒輪齒數及帶輪直徑;繪制傳動系統(tǒng)圖。其次,根據車床類型和電動機功率,確定主軸及各傳動件的計算轉速,初定傳動軸直徑、齒輪模數,確定傳動帶型號及根數,摩擦片尺寸及數目;裝配草圖完成后要驗算傳動件(傳動軸、主軸、齒輪、滾動軸承)的剛度、強度或壽命。最后,完成運動設計和動力設計后,要將主傳動方案“結構化” ,設計主軸變速箱裝配圖及零件圖,側重進行傳動軸組件、主軸組件、變速機構、箱體、潤滑與密封、傳動軸及滑移齒輪零件的設計。關鍵詞:主軸箱,無級調速,傳動系統(tǒng) IIAbstractLathe gearbox design major, mainly includes three aspects of the design, namely: the title given according to the design purpose lathe, specifications, spindle speed limit, the speed or the number of columns common ratio series, other relevant motion parameters to determine the selected spindle levels speed value; analysis and comparison, selecting transmission scheme; prepare formula or network structure, develop speed; determining a gear and pulley diameter; transmission drawn map. Secondly, according to the type of lathe and motor power, determined that the calculated spindle speed and various transmission parts, an initial shaft diameter modulus gear, belt model and determine the number, size and number of friction plates; after the completion of assembly sketch to checking the transmission member (shaft, spindle, gear, bearing) stiffness, strength or lifetime. Finally, after the completion of design and dynamic design movement, to the main drive program “structured“ designed spindle gearbox assembly drawings and part drawings, conduct focus drive shaft assembly, spindle assembly, the transmission mechanism, housing, lubrication and sealing, transmission slip gear shaft and parts of the design.Keywords: headstock, variable speed, driveIII目 錄摘要 IABSTRACT.II1 緒論 11.1 選題背景(含國內外相關研究綜述及評價)與意義 .11.2 國內外相關研究綜述 11.3 數控技術的應用與發(fā)展 21.3.1 數控車床與發(fā)展趨勢 .21.3.2 數控技術 .31.3.3 數控技術發(fā)展趨勢 52 設計計算 82.1 機床的主參數 82.2 主運動參數 82.3 切削力的計算 83 主動參數參數的擬定 103.1 主運動調速范圍的確定、計算各軸計算轉速、功率和轉矩 103.2 主電動機的選擇 114 主傳動系統(tǒng)設計 134.1 主變速方案擬定 134.2 變速結構式、結構網的選擇 134.2.1 確定變速組及各變速組中變速副的數目 .134.2.2 結構網的擬定 .144.2.3 結構式的擬定 .144.2.4 結構式的擬定 .144.2.5 確定各變速組變速副齒數 .155 傳動件的設計 165.1 帶傳動設計 165.2 選擇帶型 175.3 確定帶輪的基準直徑并驗證帶速 175.4 確定中心距離、帶的基準長度并驗算小輪包角 185.5 確定帶的根數 Z .195.6 確定帶輪的結構和尺寸 195.7 確定帶的張緊裝置 195.8 計算壓軸力 195.9 各變速組齒輪模數的確定和校核 215.9.1 齒輪模數的確定 .215.9.2 齒寬的確定 .255.9.3 齒輪結構的設計 .255.10 傳動軸的直徑估算 27IV5.10.1 確定各軸轉速 .275.10.2 傳動軸直徑的估算:確定各軸最小直徑 275.10.3 鍵的選擇 .285.11 傳動軸的校核 285.11.1 傳動軸的校核 .295.11.2 鍵的校核 .295.12 摩擦離合器的選擇和計算 305.13 齒輪校驗 325.13.1 校核 a 變速組齒輪 .335.13.2 校核 b 變速組齒輪 .345.13.3 校核 c 變速組齒輪 .365.14 軸承的選用與校核 375.14.1 各軸軸承的選用 .375.14.2 各軸軸承的校核 .375.15 主軸組件設計 38總結與展望 48參考文獻 49致 謝 5011 緒論1.1 選題背景(含國內外相關研究綜述及評價)與意義目前,我國車床的發(fā)展不僅從技術水平上已研制出五坐標的數控車床加工中心,CNC 系統(tǒng)和自動編程系統(tǒng)等。同時,也擁有了一定數量的數控車床的開發(fā)、生產、使用以及擁有量等都與世界上的先進國家有較大差距。要達到世界先進水平,迅速發(fā)展我國數控車床行業(yè)勢在必行。普通車床雖然可以進行單件、小批量生產。但解決多品種、特別是形狀復雜、精度要求高的零件。就顯得力不從心了。這時只能依賴高素質的技術工人,但產量上不去。如果一般技術工人就能完成且要上數量,就必須借助數控車床。本設計為立式車床變速箱設計,它是數控車床機械傳動部分的核心。通過改造,大大改善了車床的加工性能:自動化程度提高,減輕操作者的勞動強度,改善了勞動條件;提高加工精度,加工質量穩(wěn)定;提高生產效率;易于建立計算機通訊網絡。1.2 國內外相關研究綜述數控車床代表著機械制造業(yè)現代科學技術發(fā)展的方向和水平。目前,我國數控車床的發(fā)展不僅從技術水平上已研制出五坐標的數控車床加工中心,CNC系統(tǒng)和自動編程系統(tǒng)等。同時,也擁有了一定數量的數控車床的開發(fā)、生產、使用以及擁有量等都與世界上的先進國家有較大差距。要達到世界先進水平,迅速發(fā)展我國數控車床行業(yè)勢在必行。經濟型數控車床設計的必然性:數控車床能較好地解決形狀復雜、精密、小批多變零件的加工問題。能夠穩(wěn)定加工質量和提高生產率,也具有適應性強、較高的加工精度。但是應用數控車床還受到其它條件的限制。價格昂貴,一次性投資巨大,對于中小企業(yè)心有余而力不足。目前各企業(yè)都有大量的通用車床,完全用數控車床代替根本不可能,而且替代下來的車床閑置起來,又會造成浪費。在國內,訂購新數控車床的交貨期一般較長,往往不能滿足生產急需。通用數控車床對具體生產有多功能。要較好地解決上述問題,應走經濟型數控車床設計之路.經濟型車床設計的優(yōu)點:經濟型數控車床設計一般指對普通車床其某些部位做一定的設計,配上數控裝置,從而使車床具有數控加工能力,其目的有以下幾點:2從提高資本效率出發(fā),改造閑置舊設備,發(fā)揮車床的原有功能和改造后的新增功能,提高車床的使用價值。所有這些目的都圍繞提高車床的性能價格比,用較少的價格,得到較高的車床性能。因此,經濟型數控車床設計具有以下優(yōu)點:易于對現有車床實現自動化,而且專業(yè)性強,沒有多余功能;減少輔助加工時間,提高車床的生產效率;降低工人技術等級的要求;費用低,可充分利用原有車床設備;周期短,可滿足生產急需。1.3 數控技術的應用與發(fā)展1.3.1 數控車床與發(fā)展趨勢(1)數控車床:1946 年誕生了世界上第一臺電子計算機,這表明人類創(chuàng)造了可增強和部分代替腦力勞動的工具。它與人類在農業(yè)、工業(yè)社會中創(chuàng)造的那些只是增強體力勞動的工具相比,起了質的飛躍,為人類進入信息社會奠定了基礎。6 年后,即在 1952 年,計算機技術應用到了車床上,在美國誕生了第一臺數控車床。從此,傳統(tǒng)車床產生了質的變化。近半個世紀以來,數控系統(tǒng)經歷了兩個階段和六代的發(fā)展。①數控(NC)階段(1952~1970 年)早期計算機的運算速度低,對當時的科學計算和數據處理影響還不大,但不能適應車床實時控制的要求。人們不得不采用數字邏輯電路“搭“ 成一臺車床專用計算機作為數控系統(tǒng),被稱為硬件連接數控(HARD-WIRED NC) ,簡稱為數控(NC ) 。隨著元器件的發(fā)展,這個階段歷經了三代,即 1952 年的第一代--電子管;1959 年的第二代-- 晶體管;1965 年的第三代--小規(guī)模集成電路。②計算機數控(CNC)階段(1970 年~現在) 到 1970 年,通用小型計算機業(yè)已出現并成批生產。于是將它移植過來作為數控系統(tǒng)的核心部件,從此進入了計算機數控(CNC )階段(把計算機前面應有的“ 通用 “兩個字省略了) 。到 1971 年,美國 INTEL 公司在世界上第一次將計算機的兩個最核心的部件-- 運算器和控制器,采用大規(guī)模集成電路技術集成在一塊芯片上,稱之為微處理器(MICROPROCESSOR) ,又可稱為中央處理單元(簡稱 CPU) 。到 1974 年微處理器被應用于數控系統(tǒng)。這是因為小型計算機功能太強,控3制一臺車床能力有富裕(故當時曾用于控制多臺車床,稱之為群控) ,不如采用微處理器經濟合理。而且當時的小型機可靠性也不理想。早期的微處理器速度和功能雖還不夠高,但可以通過多處理器結構來解決。由于微處理器是通用計算機的核心部件,故仍稱為計算機數控。 到了 1990 年,PC 機(個人計算機,國內習慣稱微機)的性能已發(fā)展到很高的階段,可以滿足作為數控系統(tǒng)核心部件的要求。數控系統(tǒng)從此進入了基于PC 的階段??傊嬎銠C數控階段也經歷了三代。即 1970 年的第四代--小型計算機;1974 年的第五代--微處理器和 1990 年的第六代-- 基于 PC(國外稱為 PC-BASED) 。還要指出的是,雖然國外早已改稱為計算機數控(即 CNC)了,而我國仍習慣稱數控(NC) 。所以我們日常講的“數控“ ,實質上已是指“計算機數控“ 了。1.3.2 數控技術隨著計算機、微電子、信息、自動控制、精密檢測及機械制造技術的高速發(fā)展,車床數控技術有了長足的進步。近幾年一些相關技術的發(fā)展,如刀具及新材料的發(fā)展,主軸伺服和進給伺服、超高速切削等技術的發(fā)展,以及對機械產品質量的要求越來越高等,加速了數控車床的發(fā)展。目前數控車床正朝著高速度、高精度、高工序集中度、高復合化和高可靠性等方向發(fā)展。世界數控技術及其裝備發(fā)展趨勢主要體現在以下幾個方面。① 高速高效高精度高生產率。由于數控裝置及伺服系統(tǒng)功能的改進,主軸轉速和進給速度大大提高,減少了切削時間和非切削時間。加工中心的進給速度已達到80m/min~120m/min,進給加速度達 9.8m/s2~19.6m/s2,換刀時間小于 1s。高加工精度。以前汽車零件精度的數量級通常為 10 μm,對精密零件要求為 1 μm,隨著精密產品的出現,對精度要求提高到 0.1 μm,有些零件甚至已達到0.01 μm,高精密零件要求提高車床加工精度,包括采用溫度補償等。微機電加工,其加工零件尺寸大小一般在 1mm 以下,表面粗糙度為納米數量級,要求數控系統(tǒng)能直接控制納米車床。②柔性化柔性化包括兩個方面的柔性:一是數控系統(tǒng)本身的柔性,數控系統(tǒng)采用模4塊化設計,功能覆蓋面大,便于不同用戶的需求;二是 DNC 系統(tǒng)的柔性,同一 DNC 系統(tǒng)能夠依據不同生產流程的要求,使物料流和信息流自動進行動態(tài)調整,從而最大限度地發(fā)揮 DNC 系統(tǒng)的效能。③工藝復合化和多軸化數控車床的工藝復合化,是指工件在一臺車床上裝夾后,通過自動換刀、旋轉主軸頭或旋轉工作臺等各種措施,完成多工序、多表面的復合加工。已經出現了集鉆、鏜、銑功能于一身的數控車床,可完成鉆、鏜、銑、擴孔、鉸孔、攻螺紋等多工序的復合數控加工中心,以及車削加工中心,鉆削、磨削加工中心,電火花加工中心等。此外數控技術的進步也提供了多軸控制和多軸聯動控制功能。④ 實時智能化早期的實時系統(tǒng)通常針對相對簡單的理想環(huán)境,其作用是如何調度任務,以確保任務在規(guī)定期限內完成。而人工智能,則試圖用計算模型實現人類的各種智能行為。科學發(fā)展到今天,實時系統(tǒng)與人工智能已實現相互結合,人工智能正向著具有實時響應的更加復雜的應用領域發(fā)展,由此產生了實時智能控制這一新的領域。在數控技術領域,實時智能控制的研究和應用正沿著幾個主要分支發(fā)展,如自適應控制、模糊控制、神經網絡控制、專家控制、學習控制、前饋控制等。例如,在數控系統(tǒng)中配置編程專家系統(tǒng)、故障診斷專家系統(tǒng)、參數自動設定和刀具自動管理及補償等自適應調節(jié)系統(tǒng);在高速加工時的綜合運動控制中引入提前預測和預算功能、動態(tài)前饋功能;在壓力、溫度、位置、速度控制等方面采用模糊控制,使數控系統(tǒng)的控制性能大大提高,從而達到最佳控制的目的。⑤ 結構新型化20 世紀 90 年代一種完全不同于原來數控車床結構的新型數控車床被開發(fā)成功。這種新型數控車床被稱為“6 條腿”的加工中心或稱虛擬軸車床(有的還稱為并聯車床) ,它能在沒有任何導軌和滑臺的情況下,采用能夠伸縮的“6 條腿”( 伺服軸 )支撐并聯,并與安裝主軸頭的上平臺和安裝工件的下平臺相連。它可實現多坐標聯動加工,其控制系統(tǒng)結構復雜,加工精度、加工效率較普通加工中心高 2~10 倍。這種數控車床的出現將給數控車床技術帶來重大變革和創(chuàng)新。5⑥ 編程技術自動化隨著數控加工技術的迅速發(fā)展,設備類型的增多,零件品種的增加以及零件形狀的日益復雜,迫切需要速度快、精度高的編程,以便于對加工過程的直觀檢查。為彌補手工編程和 NC 語言編程的不足,近年來開發(fā)出多種自動編程系統(tǒng),如圖形交互式編程系統(tǒng)、數字化自動編程系統(tǒng)、會話式自動編程系統(tǒng)、語音數控編程系統(tǒng)等,其中圖形交互式編程系統(tǒng)的應用越來越廣泛。圖形交互式編程系統(tǒng)是以計算機輔助設計(CAD)軟件為基礎,首先形成零件的圖形文件,然后再調用數控編程模塊,自動編制加工程序,同時可動態(tài)顯示刀具的加工軌跡。其特點是速度快、精度高、直觀性好、使用簡便,已成為國內外先進的CAD/CAM 軟件所采用的數控編程方法。目前常用的圖形交互式軟件有 Master CAM、Cimatron、Pro/E、UG、CAXA、Solid Works 、CATIA 等。⑦ 集成化數控系統(tǒng)采用高度集成化芯片,可提高數控系統(tǒng)的集成度和軟、硬件運行速度,應用平板顯示技術可提高顯示器性能。平板顯示器(FPD)具有科技含量高、質量小、體積小、功耗低、便于攜帶等優(yōu)點,可實現超大規(guī)模顯示,成為與CRT 顯示器抗衡的新興顯示器,是 21 世紀顯示器主流。它應用先進封裝和互連技術,將半導體和表面安裝技術融于一體,通過提高集成電路密度,減小互連長度和數量來降低產品價格、改進性能、減小組件尺寸、提高系統(tǒng)的可靠性。⑧ 開放式閉環(huán)控制模式采用通用計算機組成的總線式、模塊化、開放、嵌入式體系結構,便于裁減、擴展和升級,可組成不同檔次、不同類型、不同集成程度的數控系統(tǒng)。閉環(huán)控制模式是針對傳統(tǒng)數控系統(tǒng)僅有的專用型封閉式開環(huán)控制模式提出的。由于制造過程是一個有多變量控制和加工工藝綜合作用的復雜過程,包括諸如加工尺寸、形狀、振動、噪聲、溫度和熱變形等各種變化因素,因此,要實現加工過程的多目標優(yōu)化,必須采用多變量的閉環(huán)控制,在實時加工過程中動態(tài)調整加工過程變量。在加工過程中采用開放式通用型實時動態(tài)全閉環(huán)控制模式,易于將計算機實時智能技術、多媒體技術、網絡技術、CAD/CAM、伺服控制、自適應控制、動態(tài)數據管理及動態(tài)刀具補償、動態(tài)仿真等高新技術融于一體,構成嚴密的制造過程閉環(huán)控制體系,從而實現集成化、智能化、網絡化。61.3.3 數控技術發(fā)展趨勢(1)數控技術裝備工業(yè)的技術水平和現代化程度決定著整個國民經濟的水平和現代化程度,數控技術及裝備是發(fā)展新興高新技術產業(yè)和尖端工業(yè)(如信息技術及其產業(yè)、生物技術及其產業(yè)、航空、航天等國防工業(yè)產業(yè))的使能技術和最基本的裝備。馬克思曾經說過“各種經濟時代的區(qū)別,不在于生產什么,而在于怎樣生產,用什么勞動資料生產” 。制造技術和裝備就是人類生產活動的最基本的生產資料,而數控技術又是當今先進制造技術和裝備最核心的技術。當今世界各國制造業(yè)廣泛采用數控技術,以提高制造能力和水平,提高對動態(tài)多變市場的適應能力和競爭能力。此外世界上各工業(yè)發(fā)達國家還將數控技術及數控裝備列為國家的戰(zhàn)略物資,不僅采取重大措施來發(fā)展自己的數控技術及其產業(yè),而且在“高精尖”數控關鍵技術和裝備方面對我國實行封鎖和限制政策??傊?,大力發(fā)展以數控技術為核心的先進制造技術已成為世界各發(fā)達國家加速經濟發(fā)展、提高綜合國力和國家地位的重要途徑。數控技術是用數字信息對機械運動和工作過程進行控制的技術,數控裝備是以數控技術為代表的新技術對傳統(tǒng)制造產業(yè)和新興制造業(yè)的滲透形成的機電一體化產品,即所謂的數字化裝備,其技術范圍覆蓋很多領域:(1)機械制造技術;(2)信息處理、加工、傳輸技術;(3) 自動控制技術;(4) 伺服驅動技術:(5)傳感器技術:(6)軟件技術等。(2)數控技術的發(fā)展趨勢數控技術的應用不但給傳統(tǒng)制造業(yè)帶來了革命性的變化,使制造業(yè)成為工業(yè)化的象征,而且隨著數控技術的不斷發(fā)展和應用領域的擴大,他對國計民生的一些重要行業(yè)(IT、汽車、輕工、醫(yī)療等 )的發(fā)展起著越來越重要的作用,因為這些行業(yè)所需裝備的數字化已是現代發(fā)展的大趨勢。從目前世界上數控技術及其裝備發(fā)展的趨勢來看,其主要研究熱點有以下幾個方面。①高速、高精加工技術是裝備的新趨勢效率、質量是先進制造技術的主體。高速、高精加工技術可極大地提高效率,提高產品的質量和檔次,縮短生產周期和提高市場競爭能力。為此日本先端技術研究會將其列為 5 大現代制造技術之一,國際生產工程學會(CIRP) 將其確定 21 世紀的中心研究方向之一。在轎車工業(yè)領域,年產 30 萬輛的生產節(jié)拍是 40 秒/輛,而且多品種加工是7轎車裝備必須解決的重點問題之一;在航空和宇航工業(yè)領域,其加工的零部件多為薄壁和薄筋,剛度很差,材料為鋁或鋁合金,只有在高切削速度和切削力很小的情況下,才能對這些筋、壁進行加工。近來采用大型整體鋁合金坯料“掏空”的方法來制造機翼、機身等大型零件來替代多個零件通過眾多的鉚釘、螺釘和其他聯結方式拼裝,使構件的強度、剛度和可靠性得到提高。這些都對加工裝備提出了高速、高精和高柔性的要求。目前高速加工中心進給速度可達 80m/min,甚至更高,空運行速度可達100m/min 左右。目前世界上許多汽車廠,包括我國的上海通用汽車公司,己經采用以高速加工中心組成的生產線部分替代組合車床。美國 CINCINNAT 工公司的 HyperMach 車床進給速度最大達 60m/min,快速為 100m/min,加速度達2g,主軸轉速已達 60000r/min。加工一薄壁飛機零件,只用 30min,而同樣的零件在一般高速車床加工需 3h,在普通車床加工需 8h;德國 DMG 公司的雙主軸車床的主軸速度及加速度分別達 12000r/mm在加工精度方面,近 10 年來,普通級數控車床的加工精度已由 l0um 提高到 5} m,精密級加工中心則從 3}5um,提高到 1 一 1.5}m,并且超精密加工精度已開始進入納米級。在可靠性方面,國外數控裝置的 MTBF 值己達 6000h 以上,伺服系統(tǒng)的MTBF 值達到 30000h 以上,表現出非常高的可靠性。為了實現高速、高精加工,與之配套的功能部件如電主軸、直線電機得到了快速的發(fā)展,應用領域進一步擴大。②智能化、開放式、網絡化成為當代數控系統(tǒng)發(fā)展的主要趨勢21 世紀的數控裝備將是具有一定智能化的系統(tǒng),智能化的內容包括在數控系統(tǒng)中的各個方面:為追求加工效率和加工質量方面的智能化,如加工過程的自適應控制,工藝參數自動生成;為提高驅動性能及使用連接方便的智能化,如前饋控制、電機參數的自適應運算、自動識別負載自動選定模型、自整定等;簡化編程、簡化操作方面的智能化,如智能化的自動編程、智能化的人機界面等;還有智能診斷、智能監(jiān)控方面的內容、方便系統(tǒng)的診斷及維修等。③數控設備更注重安全性、操作性數控設備是集機電一體化的產品,由于其自動化程度高,所以對其安全性和可操作性有了更高的要求。892 設計計算2.1 機床的主參數設計一臺數控臥式重型車床主傳動系統(tǒng),主軸轉速范圍 0.5~71rpm,床身上工件最大回轉直徑 2000mm,刀架上最大切削力 15kN,頂尖間最大加工工件重量200T,頂尖間最大加工工件有效長度 15000mm,主軸前后徑向軸承為恒流靜壓軸承。2.2 主運動參數根據任務書主軸的轉速范圍為 0.5-71/min.2.3 切削力的計算由于切削過程的復雜性,并且影響它的因素又多,因此目前尚未導出簡便計算進給力、徑向力、切削力 的理論公式,一般都是通過大量實驗,由測力儀得到切削力后進行數據處理,建立經驗公式。在建立經驗公式時,大多數都是將背吃刀量、進給量及切削速度這三個主要因素作為可變因素,而其它影響因素則用修正系數間接計算,從而得出、、 三個分力的計算公式:FX=Pαafkfvr·kvFz·krFz·kaFz·kvbFz·khFz·kuFz·kbr1FzFy =PαfkfFy·kvFy·krFy·kaFy·kvbFy·khFy·kuFy·kbr1FyFz =PαfkfFx·kvFx·krFx·kaFx·kvbFx·khFx·kuFx·kbr1Fx式中及下列各參數均是以實驗條件得出, 切削深度、進給量、切削速度以實驗條件中最大值計算, 而不是本機床實際所加工最大允許量, 詳見《機床設計手冊》:P——單位切削力 ( kgf /mm2) , 取 P=210kgf /mm2;——切削深度, 1~5mm, 取 αp=5mm;F——進給量, 0.1~0.5mm/r, 取 f=0.5mm/r;v——切削速度, 90~105m/min, 取 v=105m/min。以上取值及各修正系數源于《機床設計手冊》。經計算:P=586.3kgf據手冊,KX=0.35~0.5,取=0.43KY=0.35~0.5,取=0.43則 Px=252kgf; Py=252kgf10總切削 F==1090.5kgf=10697.8N機床切削總功率: P=10697.8×105 /(60×2000)=18.7kW按上面所列式求得切削功率后, 還需考慮機床的傳動效率, 機床的電機功率為≥Pc/ηm, 式中 ηm 為機床的傳動效率, 一般取為 0.75~0.85, 取 0.85 計算, 計算得≥=22kW。查《機械設計課程設計指導書》P178 可得,選擇電動機型號為 Y180L-4,滿載時,其轉速為 1470r/min。113 主動參數參數的擬定3.1 主運動調速范圍的確定、計算各軸計算轉速、功率和轉矩主運動調速范圍的確定(本小節(jié)公式除非特別說明,均出自資料[12])∵數控車床主軸轉速范圍 0.5~71r/min則數控車床總變速范圍 maxin140nR??估算主軸的計算轉速,由于采用的是無級調速,所以采用以下的公式:(2.3)0.30.3maxini 71()5()2r/i??A因為數控機床主軸的變速范圍大于計算轉速的實際值同時為了便于計算電機的恒功率變速范圍 d8R140p?由于 RnpRdp,電動機直接驅動主軸不能滿足恒功率變速要求,因此需要串聯一個有級變速箱,以滿足主軸的恒功率調速范圍。取 ,則 對于數控車床,為了加工端面時滿足恒6f?dp?7.1lgZnp?f?線速度切削的要求,應使轉速有一些重復,故取 Z=4故前面?zhèn)鲃颖确峙淇扇?。?Z=4, ,計算出變速齒輪箱公比 ,則??4d1a,zfpzfpR??? 25.?ff?, 取變速箱有四種傳動比: ????;1/8.2/1.??;44????;.//./ ;121??由圖 2 主軸功率特性圖中可以看出,當主軸在 71~0.5r/min 的轉速范圍內,功率段 abcde 恒功率輸出,可以實現恒功率不停車無級調速,故此車床用于加工12盤類零件時,可以恒線速度切削,嚴格保證加工質量,但以上設計沒有考慮系統(tǒng)內傳動元件造成的功率損失。3.2 主電動機的選擇根據前面的切削計算,選擇 22KW 的 Y180L-4 型三相異步電動機,參數如下圖表Y180L-4 型三相異步電動機產品型號:Y180L-4 型Y180L-4 型三相異步電動機使用條件: 環(huán)境溫度:-15℃<θ<0.5℃ 海拔:不超過 2000m 額定電壓:380V,可選 220-760V 之間任何電壓值額定頻率:50Hz、60Hz 防護等級:IP44、IP54、IP55 絕緣等級:B 級、F 級、H 級 冷卻方式:ICO141 工作方式:S1 連接方式:3KW 及以下 Y 接法、4KW 及以上為△接法 Y180L-4 型三相異步電動機特點 Y180L-4 型三相異步電動機功率:22KW 電壓:380V 電流:21.8A 絕緣:B 噪音:87 dB(A) 轉速 2900r/min 是全封閉自扇冷式鼠籠型三相異步電動機,是全國統(tǒng)一設計的基本系列,它同時是符合 JB/T9616-1999 和 IEC34-1 標準的有13關規(guī)定, 具有國際互換的特點。 Y180L-4 型三相異步電動機廣泛適用于不含易燃、易爆或腐蝕性氣體的一般場合和無特殊要求的機械設備上,如金屬切削機床、泵、風機、運輸機械、攪拌機、農業(yè)機械和食品機械等。144 主傳動系統(tǒng)設計4.1 主變速方案擬定擬定變速方案,包括變速型式的選擇以及開停、換向、制動、操縱等整個變速系統(tǒng)的確定。變速型式則指變速和變速的元件、機構以及組成、安排不同特點的變速型式、變速類型。變速方案和型式與結構的復雜程度密切相關,和工作性能也有關系。因此,確定變速方案和型式,要從結構、工藝、性能及經濟等多方面統(tǒng)一考慮。變速方案有多種,變速型式更是眾多,比如:變速型式上有集中變速,分離變速;擴大變速范圍可用增加變速組數,也可采用背輪結構、分支變速等型式;變速箱上既可用多速電機,也可用交換齒輪、滑移齒輪、公用齒輪等。顯然,可能的方案有很多,優(yōu)化的方案也因條件而異。此次設計中,我們采用集中變速型式的主軸變速箱。4.2 變速結構式、結構網的選擇結構式、結構網對于分析和選擇簡單的串聯式的變速不失為有用的方法,但對于分析復雜的變速并想由此導出實際的方案,就并非十分有效。4.2.1 確定變速組及各變速組中變速副的數目數為 Z 的變速系統(tǒng)由若干個順序的變速組組成,各變速組分別有 、?Z……個變速副。即 ? ??321Z?取 Z=4, ,計算出變速齒輪箱公比 ,則??4d1a,zfpzfpR?? 25.?ff?, 取變速箱有四種傳動比: ????;1/8.2/1.??;44????;.//./ ;121??由圖 2 主軸功率特性圖中可以看出,當主軸在 71~0.5r/min 的轉速范圍內,功率段 abcde 恒功率輸出,可以實現恒功率不停車無級調速,故此車床用于加工15盤類零件時,可以恒線速度切削,嚴格保證加工質量,但以上設計沒有考慮系統(tǒng)內傳動元件造成的功率損失。4.2.2 結構網的擬定根據中間變速軸變速范圍小的原則選擇結構網。從而確定結構網如下:4.2.3 結構式的擬定主軸的變速范圍應等于住變速傳動系中各個變速組變速范圍的乘積,即: inR?210?檢查變速組的變速范圍是否超過極限值時,只需檢查最后一個擴大組。因為其他變速組的變速范圍都比最后擴大組的小,只要最后擴大組的變速范圍不超過極限值,其他變速組就不會超過極限值。??122???PXR?4.2.4 結構式的擬定繪制轉速圖⑴、選擇 Y132S-4 型 Y 系列籠式三相異步電動機。⑵、分配總降速變速比164.2.5 確定各變速組變速副齒數齒輪齒數的確定,當各變速組的傳動比確定以后,可確定齒輪齒數。對于定比傳動的齒輪齒數可依據機械設計手冊推薦的方法確定。對于變速組內齒輪的齒數,如傳動比是標準公比的整數次方時,變速組內每對齒輪的齒數和 及zS小齒輪的齒數可以從【1】表 3-9 中選取。一般在主傳動中,最小齒數應大于18~20。采用三聯滑移齒輪時,應檢查滑移齒輪之間的齒數關系:三聯滑移齒輪的最大齒輪之間的齒數差應大于或等于 4,以保證滑移是齒輪外圓不相碰。根據【1】 ,查表 3-9 各種常用變速比的使用齒數。94P175 傳動件的設計5.1 帶傳動設計功率 P=22kW,選擇傳動比為 i=1.6計算設計功率 Pd edAdPK?表 4 工作情況系數 AK原動機ⅰ類 ⅱ類一天工作時間/h工作機 10?10~16 16?0?10~16 16?載荷平穩(wěn)液體攪拌機;離心式水泵;通風機和鼓風機() ;離心式壓縮機;7.5kW?輕型運輸機1.0 1.1 1.2 1.1 1.2 1.3載荷變動小帶式運輸機(運送砂石、谷物) ,通風機( ) ;發(fā)電機;旋7.5k?轉式水泵;金屬切削機床;剪床;壓力機;印刷機;振動篩1.1 1.2 1.3 1.2 1.3 1.4載荷變動較大螺旋式運輸機;斗式上料機;往復式水泵和壓縮機;鍛錘;磨粉機;鋸木機和木工機械;紡織機械1.2 1.3 1.4 1.4 1.5 1.6載荷變動很大破碎機(旋轉式、顎式等) ;球磨機;棒磨機;起重機;挖掘機;橡膠輥壓機1.3 1.4 1.5 1.5 1.6 1.8根據 V 帶的載荷平穩(wěn),兩班工作制(16 小時) ,查《機械設計》P 296表 4,18取 KA=1.1。即 1.24.kWdAedPK???5.2 選擇帶型普通 V 帶的帶型根據傳動的設計功率 Pd 和小帶輪的轉速 n1 按《機械設計》P297 圖 13-11 選取。根據算出的 Pd=24.2kW 及小帶輪轉速 n1=1470r/min ,查圖得:dd=80~100 可知應選取 A 型 V 帶。5.3 確定帶輪的基準直徑并驗證帶速由《機械設計》P 298表 13-7 查得,小帶輪基準直徑為 80~100mm則取 dd1=100mm ddmin.=75 mm(d d1根據 P295表 13-4 查得)表 3 V 帶帶輪最小基準直徑 mind槽型 Y Z A B C D Emind20 50 75 125 200 355 50021 2470=1.63,=10.631.9dd??所 以 由《機械設計》P 295表 13-4 查“V 帶輪的基準直徑” ,得 =160mm2d19① 誤差驗算傳動比: ( 為彈性滑21160=.3265()(%)di?????誤 ?動率)誤差 符合要求1.6325.0%10.581i?????誤 <② 帶速 147v=.3/6dnms?滿足 5m/s300mm,所以宜選用 E 型輪輻式帶輪。總之,小帶輪選 H 型孔板式結構,大帶輪選擇 E 型輪輻式結構。帶輪的材料:選用灰鑄鐵,HT200。5.7 確定帶的張緊裝置選用結構簡單,調整方便的定期調整中心距的張緊裝置。215.8 計算壓軸力由《機械設計》P303 表 13-12 查得,A 型帶的初拉力F0=130.59N,上面已得到 =153.36o,z=6,則1a1a53.72sin=60.9sinN=126ooFz???對帶輪的主要要求是質量小且分布均勻、工藝性好、與帶接觸的工作表面加工精度要高,以減少帶的磨損。轉速高時要進行動平衡,對于鑄造和焊接帶輪的內應力要小, 帶輪由輪緣、腹板(輪輻)和輪轂三部分組成。帶輪的外圈環(huán)形部分稱為輪緣,輪緣是帶輪的工作部分,用以安裝傳動帶,制有梯形輪槽。由于普通 V 帶兩側面間的夾角是 0.5°,為了適應 V 帶在帶輪上彎曲時截面變形而使楔角減小,故規(guī)定普通 V 帶輪槽角 為 32°、34°、36°、38°(按帶的型號及帶輪直徑確定) ,輪槽尺寸見表 7-3。裝在軸上的筒形部分稱為輪轂,是帶輪與軸的聯接部分。中間部分稱為輪幅(腹板) ,用來聯接輪緣與輪轂成一整體。表 普通 V 帶輪的輪槽尺寸(摘自 GB/T13575.1-92) 槽型 項目 符號 Y Z A B C D E 基準寬度 b p 5.3 8.5 11.0 14.0 19.0 27.0 32.0 基準線上槽深 h amin 1.6 2.0 2.75 3.5 4.8 8.1 9.6 基準線下槽深 h fmin 4.7 7.0 8.7 10.8 14.3 19.9 23.4 22槽間距 e 8± 0.3 12 ± 0.3 15± 0.3 19 ± 0.4 25.5± 0.5 37 ± 0.6 44.5 ± 0.7 第一槽對稱面至端面的距離 f min 6 7 9 11.5 16 23 28 最小輪緣厚 5 5.5 6 7.5 10 12 15 帶輪寬 B B =( z -1) e + 2 f z —輪槽數 外徑 d a 32° ≤ 60 - - - - - - 34° - ≤ 80 ≤ 118 ≤ 190 ≤ 315 - - 36° 60 - - - - ≤ 475 ≤ 600 38° 對應的基準直徑 d d - > 80 > 118 > 190 > 315 > 475 > 600 輪 槽 角 極限偏差 ± 1 ± 0.5 V 帶輪按腹板(輪輻)結構的不同分為以下幾種型式: (1) 實心帶輪:用于尺寸較小的帶輪(dd≤(2.5~3)d 時),如圖 7 -6a。 (2) 腹板帶輪:用于中小尺寸的帶輪(dd≤ 300mm 時),如圖 7-6b。 (3) 孔板帶輪:用于尺寸較大的帶輪((dd-d)> 100 mm 時),如圖 7 -6c 。 (4) 橢圓輪輻帶輪:用于尺寸大的帶輪(dd> 500mm 時),如圖 7-6d。(a) (b) (c) (d)圖 7-6 帶輪結構類型根據設計結果,可以得出結論:小帶輪選擇實心帶輪,如圖(a),大帶輪23選擇腹板帶輪如圖(b)5.9 各變速組齒輪模數的確定和校核5.9.1 齒輪模數的確定齒輪模數的估算。通常同一變速組內的齒輪取相同的模數,如齒輪材料相同時,選擇負荷最重的小齒輪,根據齒面接觸疲勞強度和齒輪彎曲疲勞強度條件按【5】表 7-17 進行估算模數 和 ,并按其中較大者選取相近的標準模HmF數,為簡化工藝變速傳動系統(tǒng)內各變速組的齒輪模數最好一樣,通常不超過2~3 種模數。先計算最小齒數齒輪的模數,齒輪選用直齒圓柱齒輪及斜齒輪傳動,查【4】表 10-8 齒輪精度選用 7 級精度,再由【4】表 10-1 選擇小齒輪材料為0.5C (調質) ,硬度為 280HBS:r根據【5】表 7-17;有公式:①齒面接觸疲勞強度: 32)1(1602???HPjmHznK??②齒輪彎曲疲勞強度: 34FPjF⑴、a 變速組:分別計算各齒輪模數,先計算最小齒數 28 的齒輪。①齒面接觸疲勞強度: 32)1(1602???HPjmHznK??其中: -公比 ; = 2;?P-齒輪傳遞的名義功率;P = 0.96 7.5=7.2KW;?-齒寬系數 = ;m?m105??b-齒輪許允接觸應力 , 由【5】圖 7-6 按 MQHP?lim9.HP?li線查取;-計算齒輪計算轉速;jnK-載荷系數取 1.2。=650MPa,limH?24MPaPaHP589.065????∴ mm14.302.71123 ???根據【6】表 10-4 將齒輪模數圓整為 4mm 。① 齒輪彎曲疲勞強度: 34FPjmFznK???其中: P-齒輪傳遞的名義功率;P = 0.96 7.5=7.2KW;?-齒寬系數 = ;m?m105??b-齒輪許允齒根應力 , 由【5】圖 7-11 按 MQFP?lim4.FP?li線查??;-計算齒輪計算轉速; jnK-載荷系數取 1.2。,MPaF30lim??∴ FP42.1?∴ m1.0874301 ??根據【6】表 10-4 將齒輪模數圓整為 2.5mm 。∵ 所以1FHm?41于是變速組 a 的齒輪模數取 m = 4mm,b = 32mm。軸Ⅰ上主動輪齒輪的直徑:。;; ddaa 14035128421 ????軸Ⅱ上三聯從動輪齒輪的直徑分別為:;; mmaa 9656'2'1⑵、b 變速組:確定軸Ⅱ上另兩聯齒輪的模數,先計算最小齒數 18 的齒輪。① 齒面接觸疲勞強度: 32)1(10???HPjmHznK??25其中: -公比 ; =4;?P-齒輪傳遞的名義功率;P = 0.922 7.5=6.915KW;?-齒寬系數 = ;m?m105??b-齒輪許允接觸應力 , 由【5】圖 7-6 按 MQHP?lim9.HP?li線查取;-計算齒輪計算轉速;jnK-載荷系數取 1.2。=650MPa,limH?∴ MPaPaP589.065???∴ mH 24.50213.632 ???根據【6】表 10-4 將齒輪模數圓整為 5mm 。② 齒輪彎曲疲勞強度: 34FPjmFznK???其中: P-齒輪傳遞的名義功率;P =0.922 7.5=6.915KW;?-齒寬系數 = ;m?m105??b-齒輪許允齒根應力 , 由【5】圖 7-11 按 MQ 線FP?lim4.FP?li查?。?計算齒輪計算轉速; jnK-載荷系數取 1.2。,MPaF30lim??∴ FP42.1?∴ m01.380956432 ??⑶、c 變速組:齒頂圓直徑 ; hzdaa)2+(=*1